Imagine the heart of many industries pulsating with the dynamic energy of hydraulic systems. At the heart of this technological marvel are hydraulic cylinders, critical components that function much like the muscles of the industrial world. Through their ability to extend and retract, hydraulic cylinders empower machinery to perform Herculean tasks—lifting, pushing, and pulling with astonishing force. Yet, when hydraulic cylinders fail, the repercussions are far-reaching.
It is not merely a matter of machinery coming to a standstill but a profound, emotional blow to those who depend on these systems daily. The reliability of hydraulic cylinders is foundational to the smooth operation of countless sectors, from construction to manufacturing, agriculture to mining. When these essential components falter, it signifies not just a mechanical failure, but a deep-seated disruption in workflow, confidence, and financial stability of businesses.
Hydraulic Cylinders Fail, Now What?
The failure of a hydraulic cylinder is akin to a sudden, debilitating illness striking a close family member or friend. It brings operations to a grinding halt, seeds panic and stress among the workforce, and instills a profound sense of vulnerability. Businesses and operators, who once operated with an unshakeable belief in the invincibility and reliability of their equipment, are abruptly awakened to the harsh reality of mechanical mortality.
The financial strain of unexpected repairs, downtime, and the potential loss of business and reputation is emotional. Hydraulic cylinders failing repeatedly can erode the trust in machinery that industries heavily rely on, leading to a reassessment of operational capacities and investments in maintenance and upgrades.
Contact us for reliable hydraulic repairs before your hydraulic cylinders fail.
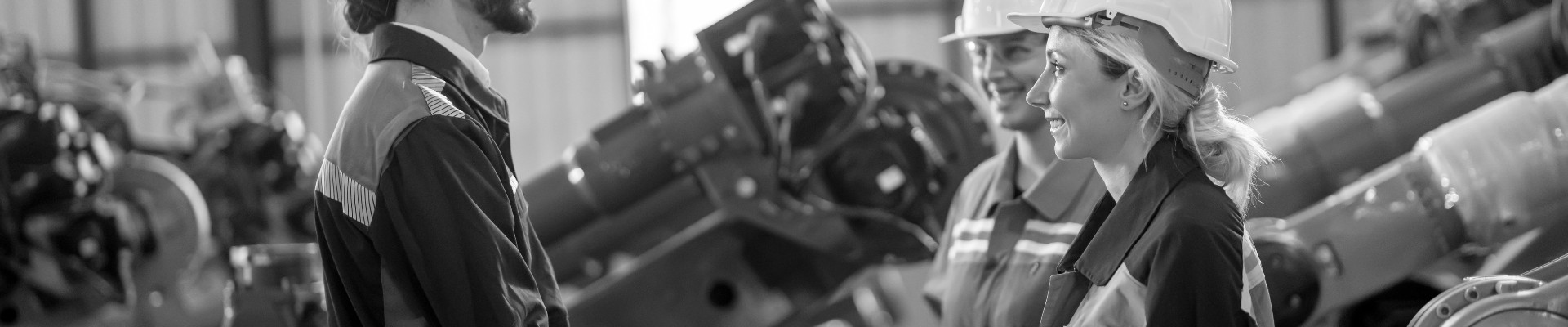
Understanding Hydraulic Cylinders
Hydraulic cylinders might be simple in concept, embodying the basic principle of using fluid pressure to produce motion, yet they encapsulate an intricate ballet of mechanical ingenuity. These devices convert the hydraulic energy into linear movement, allowing for feats of strength that defy the limitations of human capability.
However, this apparent simplicity masks a complex system of components—each of which must function in perfect synchrony. Seals, pistons, rods, and cylinders must align with precision, maintaining the integrity of the hydraulic fluid and ensuring consistent performance under varying pressures and conditions.
When hydraulic cylinders fail, it often traces back to a breakdown in this delicate ecosystem. Contaminants in the fluid, wear and tear on seals, improper alignment, or even manufacturing defects can precipitate failure, each a reminder of the intricate balance that sustains the power and efficiency of hydraulic systems.
Six Unique Reasons Why Hydraulic Cylinders Fail
1. Contamination: The Silent Killer
Contamination within hydraulic systems is an insidious issue that often goes unnoticed until it is too late. Tiny particles, invisible to the naked eye, can wreak havoc within the precision-engineered spaces of a hydraulic cylinder. This contamination is a heart-wrenching betrayal, slowly degrading the performance of hydraulic cylinders until failure is inevitable.
From dirt and dust to water and chemical contaminants, these foreign materials interfere with the hydraulic fluid’s properties, increasing wear and tear on cylinder components. The resulting damage is a mechanical failure and a significant blow to operational efficiency and reliability. As hydraulic cylinders fail due to contamination, the entire machinery’s performance is compromised, reflecting the critical importance of maintaining fluid purity and system cleanliness.
2. Seal Wear And Tear: A Slow Poison
The integrity of hydraulic cylinders is heavily reliant on the condition of their seals. These components are the guardians of a hydraulic cylinder’s functionality, keeping the fluid contained and maintaining pressure within the system. However, over time, these seals wear down. This wear and tear allows leaks to develop, diminishing the cylinder’s power and efficiency.
The gradual degradation of seals is akin to a slow poison, silently compromising the cylinder’s performance until it fails. Regular inspection and replacement of worn seals are crucial to prevent hydraulic cylinders from failing, underscoring the importance of proactive maintenance in ensuring the longevity and reliability of hydraulic systems.
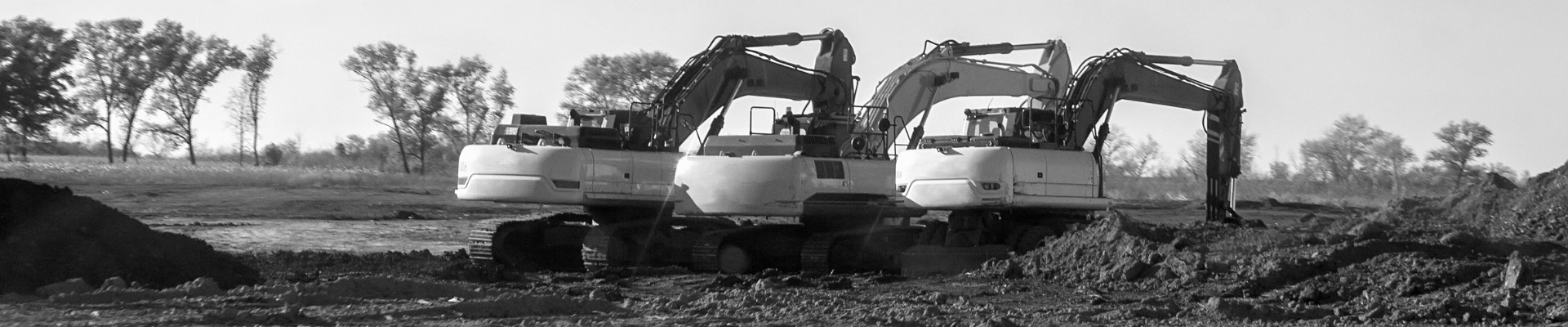
3. Cylinder Misalignment: A Misstep Towards Failure
Cylinder misalignment in hydraulic systems can be likened to a critical miscommunication between vital components, leading to strain and eventual breakdown. Even a slight misalignment can cause uneven wear and tear on the cylinder’s structure, setting the stage for premature failure. This misalignment stresses the cylinder’s rod and piston, increasing friction and resistance during operation.
As hydraulic cylinders fail due to misalignment, the efficiency and lifespan of the entire system are reduced. Ensuring proper alignment during installation and routine checks can prevent such issues, highlighting the need for meticulous attention to detail in the maintenance and operation of hydraulic systems.
4. Overloading: The Burden Too Heavy to Bear
Overloading hydraulic cylinders is an all-too-common mistake that results in significant stress and damage to the system. Asking too much of a hydraulic cylinder is akin to overburdening a trusted friend; it pushes the cylinder beyond its designed limits, leading to stress, damage, and ultimately, failure.
Overloading accelerates the wear and tear on cylinder components and increases the risk of catastrophic failure. As hydraulic cylinders fail under excessive load, they compromise the machinery’s functionality and pose safety risks to operators. Understanding and adhering to the operational limits of hydraulic cylinders are essential to prevent overloading and ensure safe and efficient performance.
5. Temperature Extremes: A Thermal Assault
Hydraulic cylinders are designed to operate within specific temperature ranges. Extreme temperatures, however, challenge the resilience of these cylinders, much like how harsh weather tests our endurance. High temperatures can cause the hydraulic fluid to thin, reducing its effectiveness and leading to leaks and decreased performance.
Conversely, extremely low temperatures can thicken the fluid, increasing the system’s workload and potentially causing damage. In either scenario, the materials within the cylinder can fail, leading to less strength and functionality. As hydraulic cylinders fail due to temperature extremes, it highlights the importance of environmental considerations in hydraulic systems design and functionality.
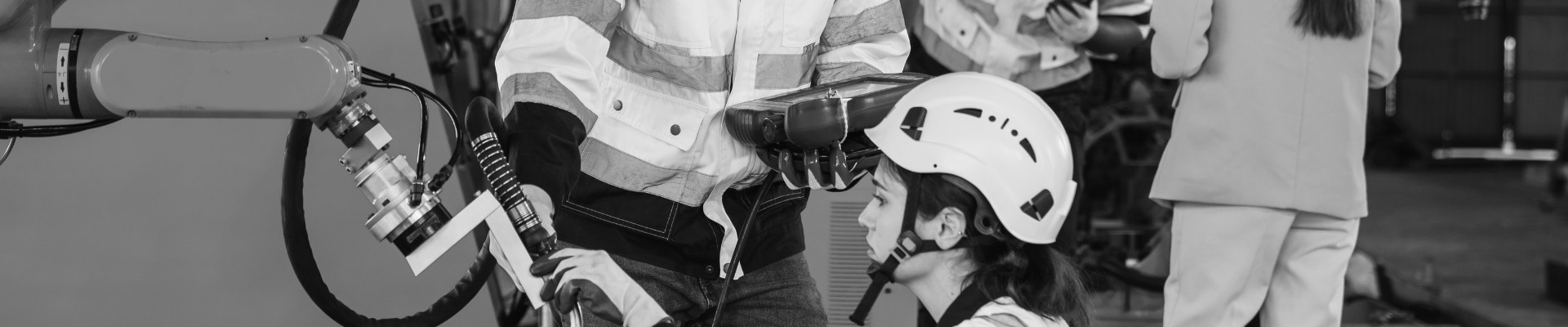
6. Manufacturing Flaws: The Hidden Imperfections
Sometimes, despite the best efforts in design and maintenance, hydraulic cylinders fail due to inherent manufacturing flaws. These hidden imperfections, often undetectable during initial inspections, can significantly impact the cylinder’s performance and durability. Inconsistencies in material quality, precision in machining parts, or errors in assembly can all lead to premature failure of the cylinder.
Such manufacturing flaws are particularly disheartening because they originate from the process meant to ensure reliability and efficiency. Recognising and addressing these flaws through stringent quality control measures and rigorous testing is essential to minimise the risk of hydraulic cylinders failing due to manufacturing defects.
Emotional Impact Of Hydraulic Cylinder Failure
The failure of a hydraulic cylinder can evoke feelings of frustration and helplessness. Operators and businesses alike experience not just the immediate stress of halted operations, but also the looming anxiety of potential future failures.
Preventive Measures to Protect Your Hydraulic Cylinders
Protecting hydraulic cylinders from failure is akin to caring for one’s health. Regular maintenance, choosing quality parts and fluids, and understanding the limits of your machinery can all help mitigate the risk of failure.
Embracing Resilience: Overcoming The Challenges Of Hydraulic Cylinder Failure
In every failure, there is a lesson. Businesses and operators who embrace resilience, learning from each setback and proactively safeguarding their equipment find success and a deeper connection to their machinery.
Understanding why hydraulic cylinders fail is mechanical insight and recognising the emotional and economic impact. By identifying the causes, we can better prepare and protect ourselves from the heartbreak of downtime and loss. Remember, in the face of adversity, resilience is our greatest strength.