Hydraulic pumps are quiet warriors in the core of many industries, providing vital processes and energy to machines. The hydraulic force required to lift, crush, and maneuvre everything from manufacturing machines to construction equipment is provided by these unsung warriors.
However, beneath their sturdy exteriors, hydraulic pumps contain weaknesses that, if disregarded, could result in catastrophic failures. Comprehending the complexities of these essential elements is not only a technical endeavour but also a crucial strategic requirement for enterprises across the globe.
Let us take a closer look at why hydraulic pumps fail.
Come along with us at Exclusive Hydraulics as we explore the reasons for the occasional malfunctions of these formidable workhorses and how understanding these issues can lead to a new level of dependability and efficiency.
Why Hydraulic Pumps Fail
Regular maintenance is the silent defender that guarantees durability and optimal performance in the world of hydraulic pumps.
1. The Value Of Continual Upkeep
Like any well-tuned machine, hydraulic pumps need regular maintenance to prevent wear and tear brought on by the demanding conditions in which they operate. This is why hydraulic pumps fail. Regular maintenance serves as more than simply a preventative measure; it is the proactive approach that guards against unanticipated disruptions and guarantees the smooth operation of hydraulic power in a variety of industrial applications.
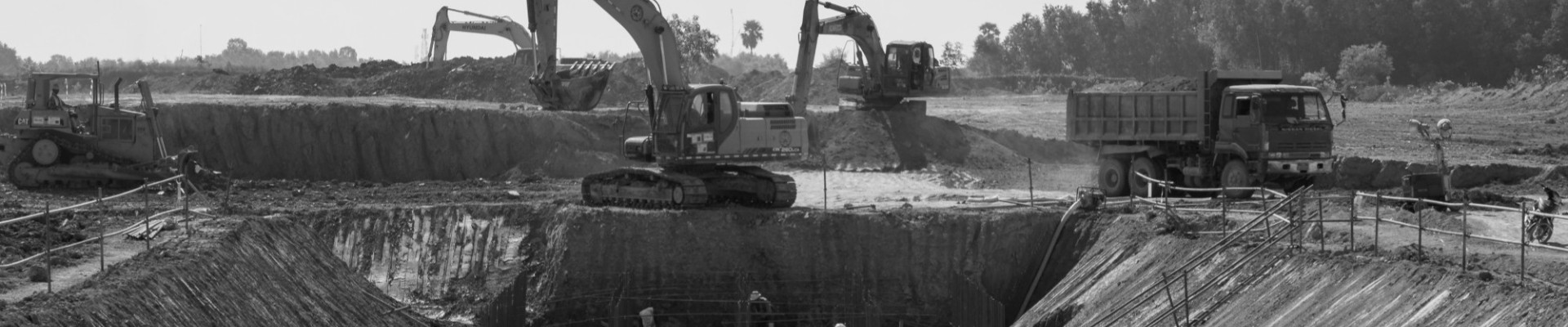
2. Common Hydraulic Pump Maintenance Tasks
Updating hydraulic pumps requires several careful procedures. Preventing problems before they get worse involves routine fluid checks and replacements, seal and O-ring inspections, and system leak detection. The resilience of hydraulic systems is largely attributed to frequent duties such as torque checks on essential components, strict adherence to prescribed fluid types, and thorough cleaning.
3. The Repercussions Of Ignoring Maintenance
Ignoring the maintenance schedule is like courting a series of problems. Contaminants seep into the system over time, jeopardising hydraulic fluid integrity and hastening the wear of essential parts. Leaks appear seals erode, and the hydraulic system as a whole is at risk of catastrophic failure.
Ignoring maintenance not only puts equipment performance at risk but also drives up operating expenses by requiring costly repairs and unscheduled downtime. When it comes to why hydraulic pumps fail, routine maintenance is an essential investment in dependability rather than a luxury.
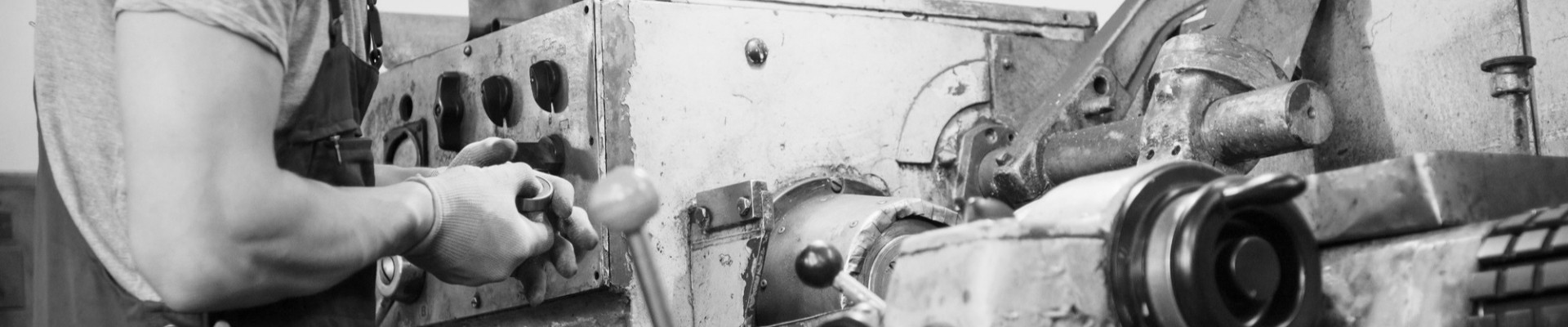
4. Problems With Contamination
Hydraulic pumps are silently vulnerable to contamination which is a big reason why hydraulic pumps fail, which reduces dependability and efficiency. Its various forms must be recognised to protect hydraulic systems.
⭐Contaminant Types
Contaminants penetrate hydraulic systems, causing wear on components and decreased fluid efficiency. These contaminants can range from abrasive particles to corrosive compounds.
⭐Effect On Pump Efficiency
Contamination raises the likelihood of breakage, wear, and damaged componentry, hence preventive actions for pump preservation are imperative.
Vibration and Misalignment:
Excessive vibration and misalignment can lead to significant issues and why hydraulic pumps fail. Vibrations can cause wear and tear on pump components, such as bearings and shafts, leading to premature failure.
Misalignment, whether due to improper installation or other factors, can result in increased stress on pump parts, reducing their operational lifespan. Regular monitoring and adjustment of alignment can help mitigate these issues.
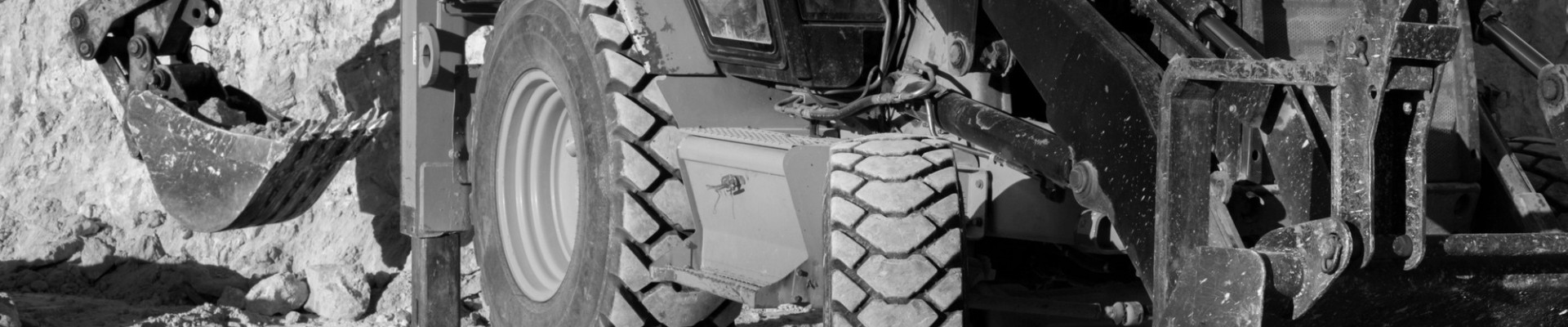
5. Seal And Gasket Failures
The integrity of seals and gaskets within a hydraulic system is crucial for preventing fluid leaks and maintaining optimal pressure levels. Over time, seals and gaskets can deteriorate due to factors like temperature extremes, pressure fluctuations, and general wear.
When these components fail, it can lead to fluid leakage, loss of pressure, and ultimately why hydraulic pumps fail. Regular inspection and replacement of worn-out seals and gaskets are essential for preventing this type of failure.
6. Cavitation
Cavitation occurs when the hydraulic fluid experiences rapid changes in pressure, leading to the formation and collapse of vapor bubbles. This phenomenon can cause damage to pump surfaces, resulting in erosion and pitting.
Over time, cavitation can compromise the efficiency and performance of the hydraulic pump, eventually being the cause of why hydraulic pumps fail.
Proper system design, maintenance, and monitoring can help minimise the risk of cavitation-related issues.
7. Chemical Incompatibility
Using incompatible hydraulic fluids or exposing pump components to corrosive chemicals can result in chemical reactions that compromise the pump’s materials.
Corrosion can lead to weakened pump structures, reduced efficiency, and eventual failure. It is crucial to ensure that the hydraulic fluid used is chemically compatible with the pump materials and that the system is not exposed to substances that can cause corrosion.
Regular fluid analysis can help identify potential chemical compatibility issues before they escalate.
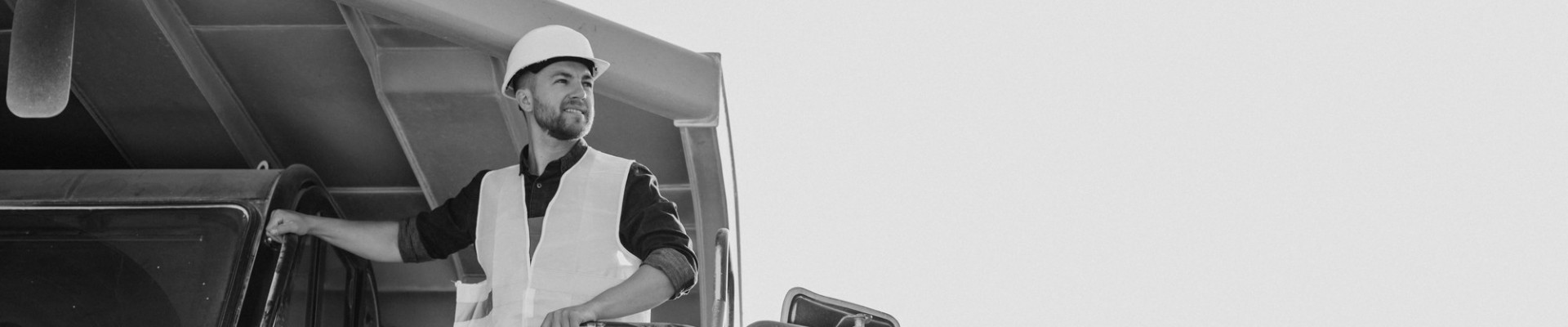
8. Lack of Temperature Control
Hydraulic pumps operate in diverse environments, and extreme temperatures can adversely affect their performance. High temperatures can lead to fluid degradation, increased wear on components, and decreased efficiency.
On the other hand, low temperatures can cause the hydraulic fluid to thicken, resulting in reduced flow and potential damage to pump internals and this is why hydraulic pumps fail. Without proper temperature control mechanisms, hydraulic pumps are susceptible to premature failure due to the challenging thermal conditions they face.
Why Hydraulic Pumps Fail & How To Avoid It
In the intricate world of hydraulic systems, understanding the vulnerabilities of pumps is paramount to ensuring their longevity and optimal functionality. Regular maintenance, addressing contamination issues, monitoring vibrations, and controlling temperature are just a few key strategies that prevent hydraulic pump failures.
Investing in proactive measures not only safeguards your equipment but also minimises unexpected downtime and reduces operational costs. As we unravel the intricacies of hydraulic pumps at Exclusive Hydraulics, we invite you to embark on a journey toward enhanced reliability and efficiency.
Are you ready to elevate your hydraulic system’s performance and reliability?
Exclusive Hydraulics is your partner in conquering the challenges that hydraulic pumps may encounter. Connect with us today to explore customised maintenance solutions, innovative technologies, and expert insights. Let us transform your hydraulic systems into resilient powerhouses that stand the test of time.
Your journey to hydraulic excellence begins now!
Read More
Visit our Blog for more updates and inspiration for hydraulic equipment, components, and repairs.